WARP STOP MOTION
TIME IS MONEY.
SAVE YOUR TIME.

RELIABILITY
First purpose of the management has always been Customer Satisfaction, with special attention to the After Sales. We place always the customer in the foreground by constantly solving and proposing targeted solutions. Our products are daily tested and overseen from our R&D and quality department within the company and in external laboratories, too, in order to improve performance and reliability day after day.
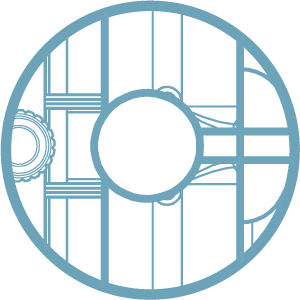
QUALITY
We are today recognized in the Textile Market for the high quality and the careful manufacture of our products. Currently, we provide with satisfaction to the biggest OEM Heald Frames & Warp Stop Motions for brands as like Vamatex, Somet, Panter, Smit, Sulzer, Itema, Sultex, Picanol, Dornier, Van de Wiele. Moreover, we collaborate with agents on foreign territories such as India, Turkey, Pakistan and we have a Sales Network extended from USA to China.
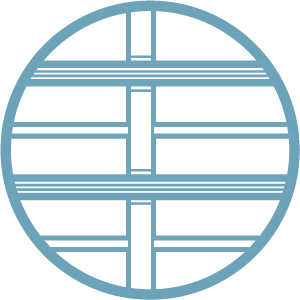
INNOVATION
The R&D department follows the market needs with special attention, with the aim of improving production processes and, above all, the functionality and reliability of the products that are daily sold all over the world. Everything is always realized closed with the Quality&Design Office for the effective compliance verification of all material and all processes in order to steadily ensure to customers the delivery of the best products.
THE PRODUCT
Quality has always been the protagonist of our warp stop motion. In all production phases, we have always considered the warp stop motion as a very important part of the loom.
The planning and the production of this device are focused on extreme weaving conditions in order to guarantee
a functional and compact warp stop motion which would be able to work under the hardest conditions.
Base Version
Standard version with broken thread finding device with lateral levers. In moving the toothed bars, the dropped wire will be visible.
Controlled Version
An electronic device mounted at the end of the contact bars, shows with a LED light the single bar and the sector in which the operator could find the dropped wire.
A625/7
The 38.5mm tube is replaced by a 50mm one, which will confer greater strength. Under the contact bars there will be 2 rods more (totally 7) where the drop wires could lean on. Heads won’t be in aluminium but made of plastic in order to cushion looms vibrations. Contact bars support is no more a unique piece but it will be divided in 2pcs. The lower part with rods is fixed and the upper one could be removed together with bars.
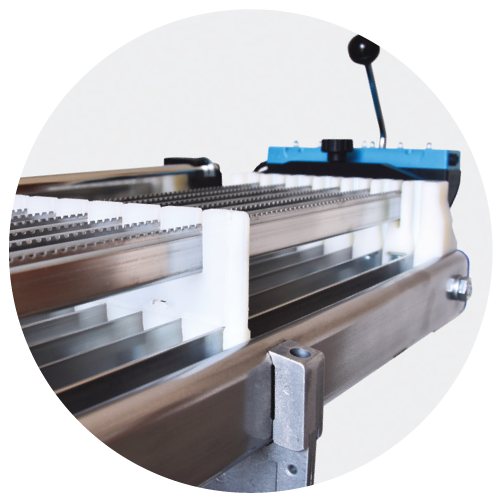
LOOP & GROUND
The new system allows the operator to be able to unlock the WSM support without using tools or specific equipment.
The guide support is bound to two steel tubes and equipped with two levers hinged to the main body by a pin. At the lower end of the levers, there is a screw with a small grip®. By acting on it, it is possible to open or close the levers, unbinding or binding the Guide Support to the tubes. Moreover, in a single WSM it could be possible to mount 2 or 4 contact bars, as needed.
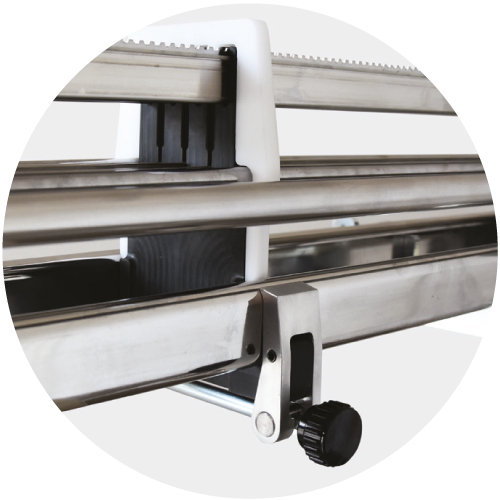
A36C + HOLD DOWN BAR
Warp Stop Motion with 6 bars, gauge 30mm. Base version or with Led control. Five drop wire separation rods D.8. Suggested model for thick and not regular yarns.
A68C + HOLD DOWN BAR
Warp Stop Motion with 8 bars, gauge 16mm. Base version or with Led control. Seven drop wire separation rods in section 18x2mm. Suggested model for thin and delicate yarns.
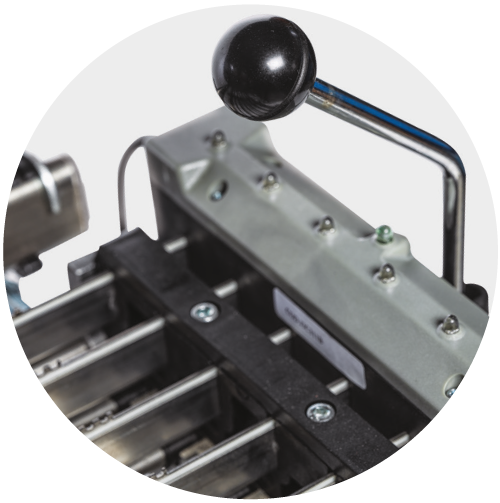
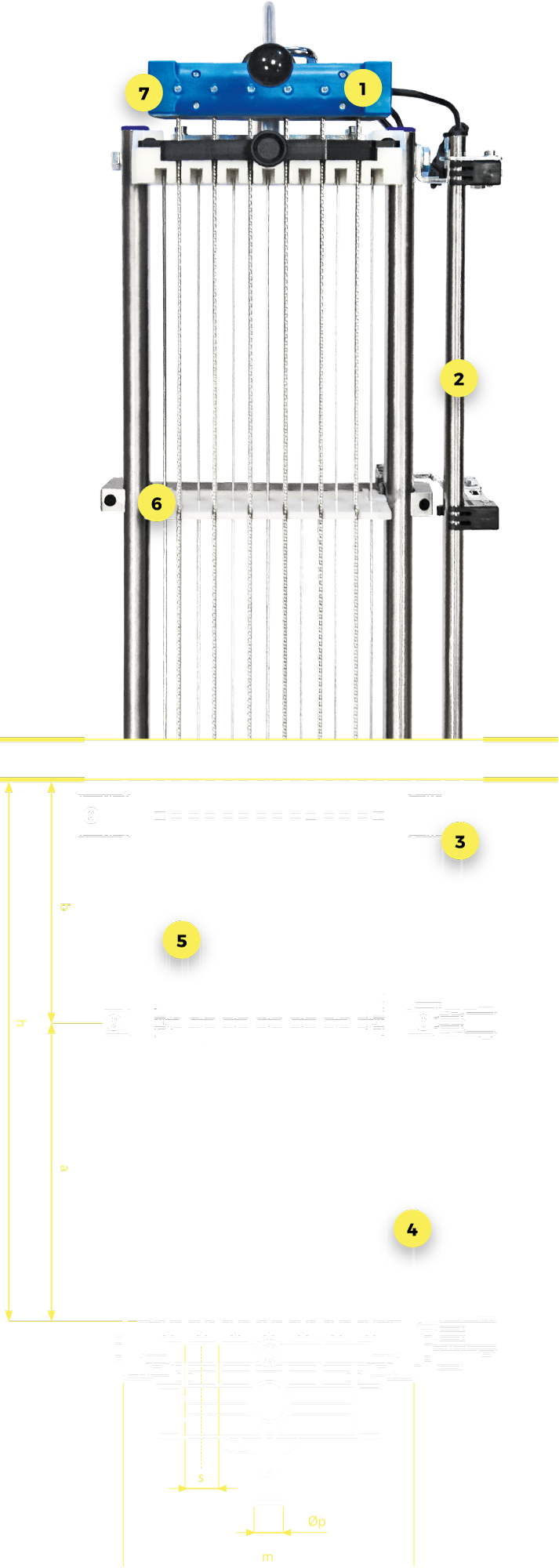
1) Optical thread breaking visualisation by LED lights, separately for the left and right side
2) Light alloy supports and stainless steel oval tubes, perfectly smoothed in order to allow the best sliding of the warp
3) Optional device Hold Down Bar which prevents the vertical opening of the yarn caused by the movement of the healds
4) Compact and strong design adaptable to all weaving machines
5) Contact bars made by antimagnetic stainless steel (material that prevents rust) insulated with polyester, the result of a tested construction technique
6) Practical and easy adjustment of the contact bars height and oval tubes
7) Optional device CFC able to indicate when the broken thread belongs to the waste selvedge